What is a CDMS? A CDMS (also referred to as CDS) is the abbreviated term for ‘Chromatographic Data Management System’, the software used to generate chromatographic raw data from the instrument and enable the analyst to process results.
With LC (liquid chromatography and GC (gas chromatography) remaining critical analytical techniques performed in Pharmaceuticals QC and R&D laboratories, the choice and configuration of the equipment and CDMS can make a big impact on the level of OECD 17, US 21CFR and EU Annex 11 compliance that is achievable.
What are the main systems used, and is there a system which could be regarded as the best?
The LC and GC market has many options for QC laboratories, but the main players are Waters®, Agilent®, Shimadzu®, Perkin Elmer® and Thermo®, each having their own CDMS which users will be recommended to use. However, modern instruments generally can connect to other CDMS systems (interoperability). One aspect which separates the systems is the type of database management systems used, with systems such as Waters® Empower™ and Thermo Scientific® ‘s ChromeleonTM using Oracle servers are far more powerful than SQL – servers, and this becomes relevant in large laboratories.
Becomes relevant in large laboratories where many instruments are running simultaneously and the CDMS is being used to process results by large numbers of users at the same time.
What makes a laboratory’s chromatographic systems compliant to current requirements?
From a QA’s perspective, the key is to look at the approach taken by the laboratory, and what that approach means in terms of OECD 17, US 21CFR Part 11, EU Annex 11, and PIC/S data integrity compliance. This includes not only the CDMS used, but their configuration. The CDMS systems using Oracle server database technology can be configured to have a double-server – ‘base’ licence subscriptions which provides buffering between two servers should there ever be a failure, making data-loss next to impossible!
‘Standalone’ instruments can still be found in some laboratories, and if multiple standalone instruments are in use (more likely to be found in laboratories with many different manufacturers/models of chromatographic systems) it should be a warning sign. Standalone systems are not connected to any kind of server database, saving data onto the local hard drive, something which can never be compliant with regulatory requirements.
So, is it all about the equipment and software/ configuration?
Far from it! The information above describes the varying measures laboratories can go to in terms of financial investment, but ultimately the QC Manager/Site management will be responsible for deciding what is used and how the equipment and CDS are configured.
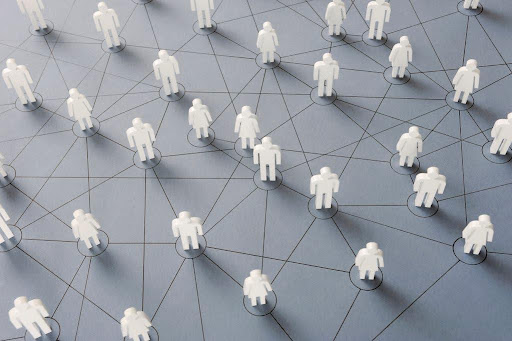
An example of good approach would be a laboratory which has all instruments linked and controllable through the same CDS system, with individual pass-word-protected user access, and varying levels of saved methods, (b) analysts who are able to change the instrument/processing method parameters and electronically check and lock results with electronic signatures, (sometimes referred to as ‘super users’) and (c) an even higher level able to create new methods, remotely oversee all system data acquisition and data processed, and of course, retrieve and review all audit trails.
Audit trails should be impossible to disable by anybody working in the laboratory and periodically reviewed separately from the usual result-audit trail checks. Processing methods audit trials can reveal any changes to a parameter, identify the use of manual integration and any other changes even though manual peak integration is something unavoidable, but a procedure should always be in place where an analyst requests authorisation to manually integrate.